2025 Colorado Real Estate Journal Conference
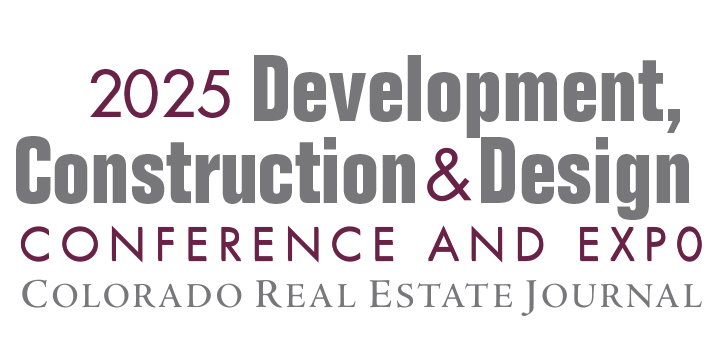
Women in Green is a platform for women and allies to gather and learn from others across fields, disciplines, generations and job titles. 2025 is going to look a little different, instead of following a theme – we want to hear from you. After 14 years of celebrating Women in Green at Greenbuild and across the country and coming off our 2024 theme Fresh Perspectives, at a critical time in our lives, your voice matters most.
Wednesday, April 2, 2025
8:30 AM-11:45 AM
Friedhoff Hall, Green Center
Colorado School of Mines
924 16th St
Golden, CO 80401
Learn more at Women in Green
Association for Preservation Technology International (APT) is offering a one day workshop at CU Denver which includes continuing education credit opportunities. More information at APTI.org.
This event is free and open to all members and non-members but please RSVP so we can better plan for snacks and refreshments!
Meet at Sloans Lake North Playground just off 26th and Tennyson for the walk at 5:30 or back at the same location at 6:30 if you just want to network!
Workplace Resource Showroom
1445 16th Street
Suite 206
Denver, CO
Map and Directions
With nearby downtown construction projects, traffic and parking can be frustrating at this time of day. WiD highly recommends alternative transportation to the event - bike, transit or ride share are great options. If using a ride share, have the driver drop off at the Thompson Hotel at 1621 Blake St across the street (the nearest Loading Zone).
On-site Valet:
Located below Marker Station, entrance on Blake.
$21-29 total
Offsite Garage Parking:
16 Market Square Garage
Alamo Plaza Garage
Sugar CubeGarage
Metered Parking:
There are meters on the surrounding streets but not recommended for this event due to the 2 hour maximum time limit.
The International Design Collection (IDC Building) is proud to host Science In Design for a special 1-day Summit June 25th! If you’re not familiar with Science in Design they are a professional educational group whose mission is to help the design industry realize its role as an alternative health resource. Dive into the science behind Neuroaesthetics, Biophilia and Fractal Design. Attendees will also learn how to market themselves as advocates for health within their field. The SiD faculty is made of scientists, architects, and marketing professionals all dedicated to teaching A&D professionals about this industry shift.
Registrants to the IDC’s Science in Design summit will also receive a free ticket to the DAM’s exhibition opening May 5th- Biophilia: Nature Reimagined. Go to the IDC Building website for more details about the day’s programming.
Join Women in Design for our annual VIP event and April First Tuesday Recess! It's time to celebrate YOU - our valued members and sponsors. Join us for our annual celebration with appetizers, drinks, live music, lots of designer SWAG, and our amazing WiD community. This event is free for WiD Members, so don't forget to sign in when registering. If you register as a non-member and then purchase a membership at the event, you'll receive $30 off the annual membership price!
Door registration will be available but only until event capacity is reached, so make sure to register in advance to secure your spot! Email widinfo@widdenver.org for any questions.
Ample parking is available in the lot at Aurum Home Technology.
The 5280 Brunch Event is back on Saturday, March 23 at Asterisk. The event will feature sweet and savory bites from local brunch spots, dedicated mimosa and Bloody Mary stations, non-alcoholic (NA) beverages, cocktails, photo booth, lounges, a DJ, and more. Plus, there is a specially priced ticket option for groups of 4+, simply select "GA - BRUNCHCREW" when purchasing tickets.
Event Type: Food + Drink Event
Details: March 23, 2024 10:00am - 1:00pm Asterisk 1075 Park Ave. W, Denver, CO 80205
Attire: Casual attire. Coat check will be available.
Ticket Details: $70 Must be 21+ to purchase tickets
Register at https://www.5280scene.com/5280-brunch-event/
WiD is pleased to be a Trade Association Partner for the Colorado Real Estate Journal’s 2024 Green Building Summit. For registration and more info, visit: https://crej.com/event/2024-green-building-summit-expo/
Date: Wednesday, May 15, 2024 (check in opens at 12:00 p.m.; program begins at 12:25 p.m.)
Location: The Cable Center, 2000 Buchtel Blvd., S., Denver, CO 80210 (just south of I-25 and
University Blvd.)
Four hours of Real Estate Continuing Education Credit have been approved.
If you have any questions about the conference, please contact Jon Stern at 303-623-1148
ext. 101 or jstern@crej.com.
By Nancy Kristof
As a member of Women in Design you get some pretty great perks, including members-only hard hat tours! Thanks to Meegan Bennett at DLR Group and WiD Membership chair extraordinaire for helping set up a tour of Hines’ new T3 mass timber spec office building in Rino!
Jessie Johnson with DLR Group provides an overview of the project and its design to Women in Design tour goers, May 2023.
T3 is an acronym for Timber, Transit and Technology. T3 Rino is one among several other T3 projects under construction, including Nashville and Houston. McCaffery and Ivanhoé Cambridge are listed as partners on the Denver project.
From afar, one might miss this six-story, 235,000-sq-ft building among the sea of cranes and high-rise construction dominating the area around RTD’s 38th & Blake station. But get up close and all five senses will tell you this is a different kind of construction site. It not only looks warm and inviting, it smells good!
Hines’ embrace of mass timber is resulting in "26 T3 projects completed, designed or in construction", according to their website.
The first T3 was completed in Minneapolis in 2016. 2019 saw T3 West Midtown Atlanta completed, which is home to Facebook, Haworth and Interior Architects, according to a 2021 news release.
The Denver T3 Rino project topped out in April of this year and is scheduled for completion later this year. A spec office building, the development is yet to secure a tenant (at least as of the time of the tour), with JLL marketing the office space and McCaffery handling retail.
The design team includes DLR as architect of record and Pickard Chilton as design architect (DLR was also involved in the Minneapolis and T3 West Midtown projects as well). Whiting-Turner is the builder. The Rino office is their second T3 project with Hines to date.
The first floor is designed with concrete, primarily to accommodate ground-floor retail and food and beverage permitting, according to Johnson. Everything above is a cross-laminated timber (CLT) system. There are three levels of parking included, but the project’s location directly across from RTD's 38th & Blake A-Line stop, makes public transportation an attractive commuting option. You’ll understand if you've tried to find street parking in Rino lately.
Starting the tour outside, DLR principal Jessie Johnson pointed out the numerous balconies cascading along the edges of the floor plates. As seen in the photo, sections with orange barriers will have curtainwall, while those without will extend to the balconies.
A view of the project from just outside the RTD 38th & Blake A-Line stop.
The first floor is dominated by the open atrium central stair. Once we ascended to the second floor we were treated to a wide open space with seemingly endless views of CLT.
The second floor balcony over the main lobby stair.
Differences and conditions specific to the use of mass timber came up often as the tour progressed. Not only is mass timber more environmentally friendly, it can often be built faster, as CLT beams and columns are typically pre-fabricated as a pre-assembled kit-of-parts brought to the site. (T3 Rino will pursue LEED Gold, Well building and Wiredscore certifications).
The optimum moisture for setting CLT is between six and 16%. Even with this spring being one of the wettest ever in Colorado our humidity still remains below that of cities such as Houston and Atlanta
There’s a total of just under 3000 pieces of timber in T3 Rino. They were setting about 25 pieces a day when erecting the structure, tour leaders said.
Wood expansion typically occurs early during construction, Johnson says, adding she’s seen it go up to an inch or an inch and half in other more humid locations such as Atlanta. But it then settles, she says. The CLT on the T3 Rino project is treated with one coat from the factory and that’s all it will get, adding the colors fade together over time.
"Column spacing on mass timber is tighter," Johnson says, noting another difference. Other components of the T3 project’s structural design included steel cross-bracing.
"One thing about wood compared to steel or concrete is the shear," Johnson says, adding, "the lateral design - timber's not as good on the shear side of things.” The solution came in steel cross bracing.
"Wood would be about twice as big around," Johnson says, explaining the choice to use steel in the cross bracing. This did present an AHJ interpretation issue, however. The city of Denver said the cross bracing did not qualify as a secondary system, deeming it a primary system, which required fireproofing of intumescent paint. Johnson points to this as a lesson learned, as not all jurisdictions interpret the structure system the same way.
Overall coordination on mass timber requires precision in the modelling and design, crediting the efforts managing the model and clash detection. "It's all going to be exposed, so you have to think really neatly how all your HVAC is going to work in the space," Johnson says.
“MEP was a big thing,” for CLT Johnson says, adding the fabricator needs to know where all the penetrations are. Out of those nearly 3000 pieces, only one beam was fabricated incorrectly.
The team also wrote a detailed tenant manual for Hines’ strict requirements on any future modifications. It includes expectation for tenant finishes or raceway or chiller line modifications, some of which is already accounted for in the original design.
Johnson noted live loading for mass timber is a little different than for concrete or steel buildings. Large assembly spaces such as anticipated break areas or conference rooms were thickened to achieve a 100 pounds per square inch load.
Hines isn’t sharing the construction cost of T3 Rino, but on average, Johnson says mass timber projects are coming in at about a 5-8% percent premium.
So why mass timber?
Its numerous benefits are getting a lot of attention: Environmentally friendly, lower embodied carbon, and it often results in faster build times. Beyond statistics, Hines seems to have faith that the kinds of spaces created by mass timber will not only help attract, but also help retain tenants. And as downtown Denver office vacancy rates continuing to hover around 25%, developers are owners are seeking advantages to help them rise above the competition.
Johnson noted surveys of tenants showed many love working in older loft-style buildings and they're often easily leased. Yet the studies also found that people would leave after a few years, citing leaky windows or inconsistent heating and cooling among their reasons. She says projects such as T3 can modernize the look and feel of these older wood-framed buildings and provide tenants with space that helps them attract the best talent.
I’m looking forward to seeing the completed space and in the meantime will await Hines’ announcement on who will be taking the space!
Project team:
Design
Architecture: DLR and Pickard Chilton
Structural Engineering: MKA
MEP: Alvine Engineering
Envelope: Morrison Hershfield
Landscape: Norris Design
Construction:
General Contractor: Whiting-Turner
Structural: Nordic Structures
Concrete: Rago
Mechanical/Plumbing: Legacy Mechanical
Electrical: Weifield Group
Framing: Heggem Lundquist
Come network and browse for plants with WiD! First Tuesday Recesses are open to non-members, so bring a friend or colleague! No RSVP required.
WiD is partnering with Colorado Real Estate Journal’s 2023 Workplace & Design Conference & Expo on Wednesday, August 23, 2023 as a Trade Association Partner. This event includes CEU opportunities.
Agenda, details and registration can be found here:
https://crej.com/event/2023-workplace-design-conference-expo/#crej-event-agenda
The Conference begins at 12:25 pm (check in opens at 12:00 pm) at the Cable Center, 2000 Buchtel Blvd, Denver, CO 80210 (just south of I-25 and University Blvd).
If you have any questions about speaking or exhibiting at the conference, please contact Jon Stern at 303-623-1148 ext. 101 or jstern@crej.com.
The conference is produced in association with:
Anderson Mason Dale Architects, Cushman & Wakefield, Newmark, Savills, JLL, Patrinely Group, Crescent Real Estate, EUA, stok, Gensler, Cresa, Elsy Studios, 3D Identity/elements, Stantec, open studio | architecture, Semple Brown Design, Boots Construction, Saunders Construction, CBRE | Project Management, Task PM, Clic Design Studio, Tryba Architects, Kieding, RATIO, DLR Group.
We hope to see you there!
August 8, 2023
Join WiD for a members only exclusive tour of the Montbello High School project led by staff from the general contractor, architecture and engineering teams. The project is a $130 million investment by Denver Public Schools to rebuild and remodel the former Montbello HS which the district voted to close in 2010. New construction of the comprehensive high school is 212,000 sf of structural precast concrete, steel, and curtain wall. Two existing gyms, the swimming pool, and the auditorium will be renovated and seamlessly incorporated into the new building.
Hard hat tours are free but spaces are limited, so snag your spot by registering today!
Event details:
Attire: This is an active construction site so personal protective equipment is required - hard hat, closed-toed shoes, safety glasses and vest. WiD has hard hats, glasses and vests available but feel free to bring your own.
Parking: Parking is available in the west parking lot, accessed off Crown Blvd, at the intersection with 50th Ave. At the far end of the lot, toward the auditorium.
Meet at Gate 3 at 3:30 PM!
Networking hour will follow the tour with at a nearby location TBD.
A full day of CEUs focused on Wellness in Design and Personal Development for Interior Designers, Architects, Custom Home Builders and Industry Professionals.
Join IDC for this special educational event that will influence your creativity forever and discover how you can be an alternative health resource for your clients. Learn more and register on IDC's website.
FTR this month will be at the annual WIC Industry event on 3/7 from 5-9 PM at Mile High Station and hosted by Mortenson. The event raises donations for three local nonprofits that promote education and careers in construction to girlsGirls Inc. of Metro Denver, STEMblazers, and Transportation & Construction Girl. This is a well attended event so WiD is asking our members to wear green so we can find one another at the event!
Registration is only $10 but closes 3/6 so get event details and register on the WIC website today!
We hope to see you there!
Hosted by Sloan, two events invite the Denver Design Community to network and fundraise for the Dumb Friends League. See below for details! Pets and Pantone Brunch Design + Dogs Happy Hour
STEMBLAZERS is a local organization with a mission to INSPIRE GIRLS TO VISUALIZE THEMSELVES IN SCIENCE, TECHNOLOGY, ENGINEERING, AND MATH PROFESSIONS with a LONG TERM GOAL TO REACH 1 MILLION GIRLS AND INFLUENCE THEM TO PURSUE A CAREER IN STEM. Check out their website and sign up for the event above here!
Click here or the image above to learn more and register.
We've been thinking about what we could do to connect our members during these crazy times and have developed two new membership amenities: a new Membership Directory and Forum. Both of these assets are live, but you must opt-in to participate and update the profile information that you would like to share in the Directory.
Here are the steps to get into the profile and gain access to the forum and directory:
1. Log in on the WiD Website. It is the button at the top.
2. Go to your membership profile, now the orange button on the top.
3. Make sure to update your information in your profile and then at the bottom click "Show Profile" to show your profile in our new member directory.
Your profile will be visible in our directory and you'll be able to use our new Forum to chat with fellow members.
4. Navigate to the Forum
5. Under "My Profile" in the Forum page update your picture and email address if you'd like it to be different than your email associated with your WiD membership.
Women are currently underrepresented in STEAM careers and Girl Scouts wants to change our future workforce pipeline by exposing and engaging girls in STEAM programs that spark their interest and increase their confidence and competence in STEAM. We invite you to support Girl Scouts in middle and high school (6-12) who want to learn more about architecture, engineering, design, and construction through our STEAM Design Challenge! Girl Scouts groups, supported by professionals in these fields, will design and construct a freestanding structure from empty cookie boxes centered around a theme of “What Girl Scouts Do”.
We are seeking professionals to act as mentors and supportive adults for Girl Scouts, as they complete the STEAM Design Challenge. Participating girls will be recruited by GSCO and you will work with your STEAM Design Team two times per month for at least 90-minute sessions. The dates and times of the sessions will be decided ahead of the program and Girl Scouts will select their groups based on the times that fit their schedules.
See the STEAM Design Challenge Team Info Flyer for more information and check out the WiD forum to organize a team.
April 15, 2022 - April 15, 2022
4817 National Western Dr
Description:
Join WiD for a hard hat tour of the Hydro building at the new CSU Spur campus. Still under construction, the Hydro building will focus on water, with Denver Water’s water quality laboratory, a connection to the South Platte River, event space, artist studios, a farm-to-table cafe and more! Following the tour, we will meet for networking happy hour nearby.
Hard hat tours are free and open to members only but space is limited and registration is required. Make sure you are logged into your WiD account to register!
Notes for attendees:
Appropriate construction wear is required for the tour - WiD will provide hard hats, vests and safety glasses for attendees. Bring your own glasses (any type of glasses are fine) and work gloves if you have some.
There is parking adjacent to the building and the tour will meet in front of the building.
Because the building is still under construction, Google maps doesn't understand the address properly but if you search directions for Stockyard Saloon, it should get you there.
The College of Architecture and Planning at CU Denver organizes a series of lectures and events that are free to the public. See the schedule here.
Habitat for Humanity is having a Gingerbread House Decorating Competition! They will provide all the supplies, you build your house, and then you’ll gather “votes” on your house by inviting peers to make donations through an online fundraising platform. If you are interested in creating a team with other WiD Members, reply to the thread in our brand new FORUM just for WiD members. More information on Habitat for Humanity of Metro Denver's website.
5280 Home Top Denver Design Event is on December 1st. RSVP at rsvp.5280.com/tdd2021
Partner Event from NEWH Rocky Mountain Chapter - Conscious Conversations, Checking In With Building Bridges
It’s been six months since the kick-off of EBECC’s Conscious Conversations series and EBECC is ready to continue this dialogue with Building Bridges for our semi-annual check-in. We will be diving deeper into DEI topics such as unconscious bias, intersectionality, privilege and oppression. This educational session would not be possible without the collaboration with NEWH Rocky Mountain Chapter, ASID Colorado Chapter, and Knoll Western Mountain Region.
Space is limited to 50 guests* to keep an intimate and intentional environment. With the positive response we’ve had to earlier sessions in this Conscious Conversation series, we anticipate selling out. Snag your spot today! Guests should be part of industries related to Denver/Colorado built environment due the nature of the discussion. Although this event is free, in order to make it equitable for all to attend, we would greatly appreciate a donation at any amount. All donations will be used to continue NEWH’s efforts to promote and educate members about diversity, equity, and inclusion – in addition to continuing to support the initiatives of EBECC. Suggested donation is $15.
August 3, 2021
Join WiD at this fun alternative to a country club to practice your golf swing, brush up on your putting skills, or just come to socialize! No golf clubs needed or BYOC.
Non-members, colleagues, friends and family welcome. RSVP for $5, which also includes a drink and an appetizer. RSVP via the website through noon on August 3rd. Payment can also be made at the door that evening.
Voices on Canvas in partnership with the Denver Museum of Nature and Science (DMNS) is looking for volunteers from WiD (and teams of 2-4 children) to participate in their 11th annual Lego Challenge. Young potential city builders use familiar LEGO building bricks to construct a model city block. The build is representative of their own vision of an ideal place to live, work and play. Each competing Team attends a LEGO Town Hall Meeting and Design Show & Tell Workshop which lays the groundwork towards discussions involving community and urban planning. Volunteers are appreciated NOW until August 10 and the individual time commitment is determined by each individual volunteer! Opportunities on July 10th, July 17th, July 31st and August 7th.
To volunteer, please call 303-329-4625 or email Kathleen@voicesoncanvas.org
Volunteer Opportunity Details Here